Vehicle Dynamics Simulation Products
Vehicle Dynamics Simulation
Mechanical Simulation produces and distributes software tools for simulating and analyzing the dynamic behavior of motor vehicles in response to steering, braking, and acceleration control inputs.
These software tools are extensively validated and correlated to real-world results as measured and observed by many automotive OEMs around the world.
Vehicle Dynamics Simulation Products
The simulation packages share many technical features: a user-friendly graphical interface and database, VS Visualizer (3D animator and plotting), and math models that have been validated by decades of research and yet run significantly faster than real time.
The vehicle simulation packages allow you to extend the models using the built-in VS Command language and/or external software such as MATLAB/Simulink, LabVIEW, C code, and others.
Furthermore, they can be run in real-time with hardware in the loop (HIL) or as driving simulators.
Vehicle Dynamics Simulation
Driving Simulation
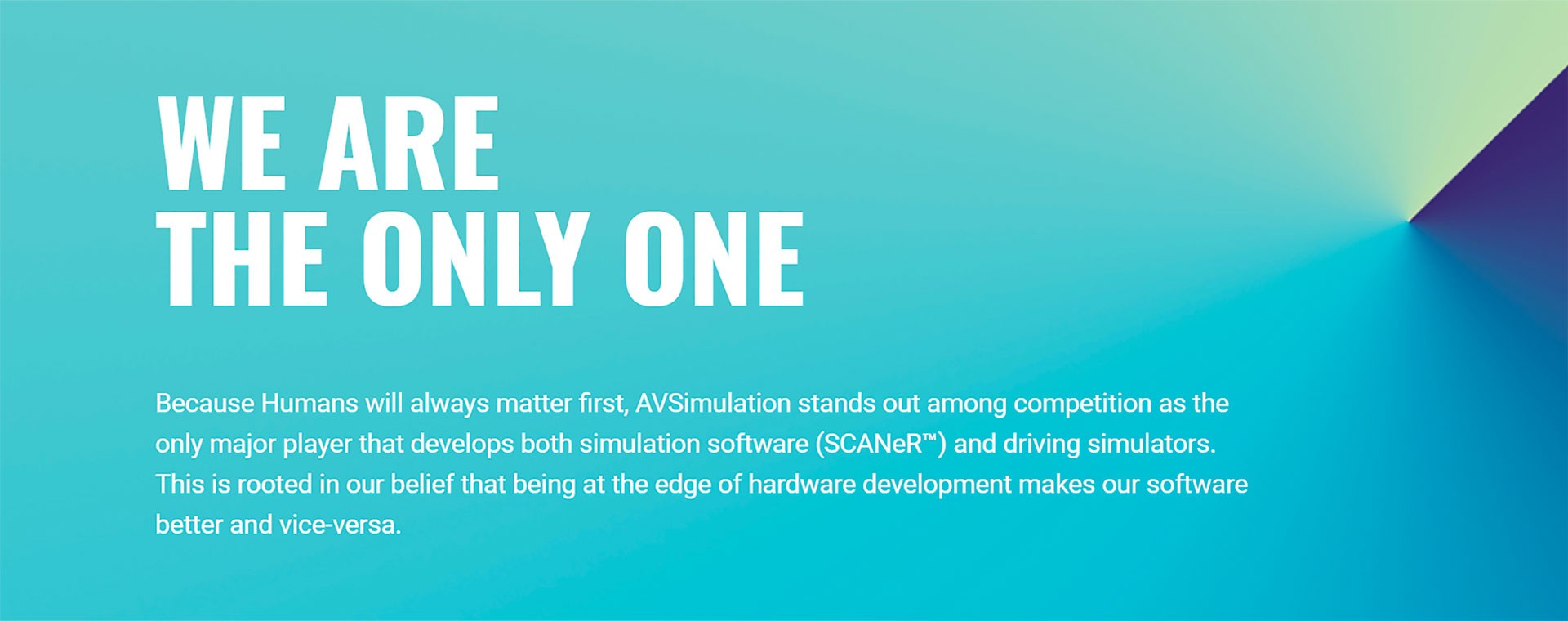
Driving an Autonomous Vehicle around a building block or on a straight highway will never expose it to the endless accident-prone possibilities and situations that it can face in particular at night or in harsh weather conditions.
This is the reason why our software solution – SCANeR – has been selected by the largest car manufacturers (in volumes) for prototyping, validation and now massive simulation on either on premise or cloud based – and nearly unlimited – GPUs and CPUs.
With the rise of autonomy and connectivity the automotive industry is undergoing the fastest transformation since Henry Ford. It has become a race where all players have to run tremendous amounts of virtual scenarios in order to test captured data and drive billions of relevant digital miles faster than competition.
AVSimulation enables its clients to accelerate thanks to end-to-end simulation solutions including SCANeR™ the most open and complete simulation platform for the automotive industry, the most advanced driving simulators as well as all the associated services required to help them focus on their experimentation.
AVSimulation
Innovate, Simulate Accelerate
Applications
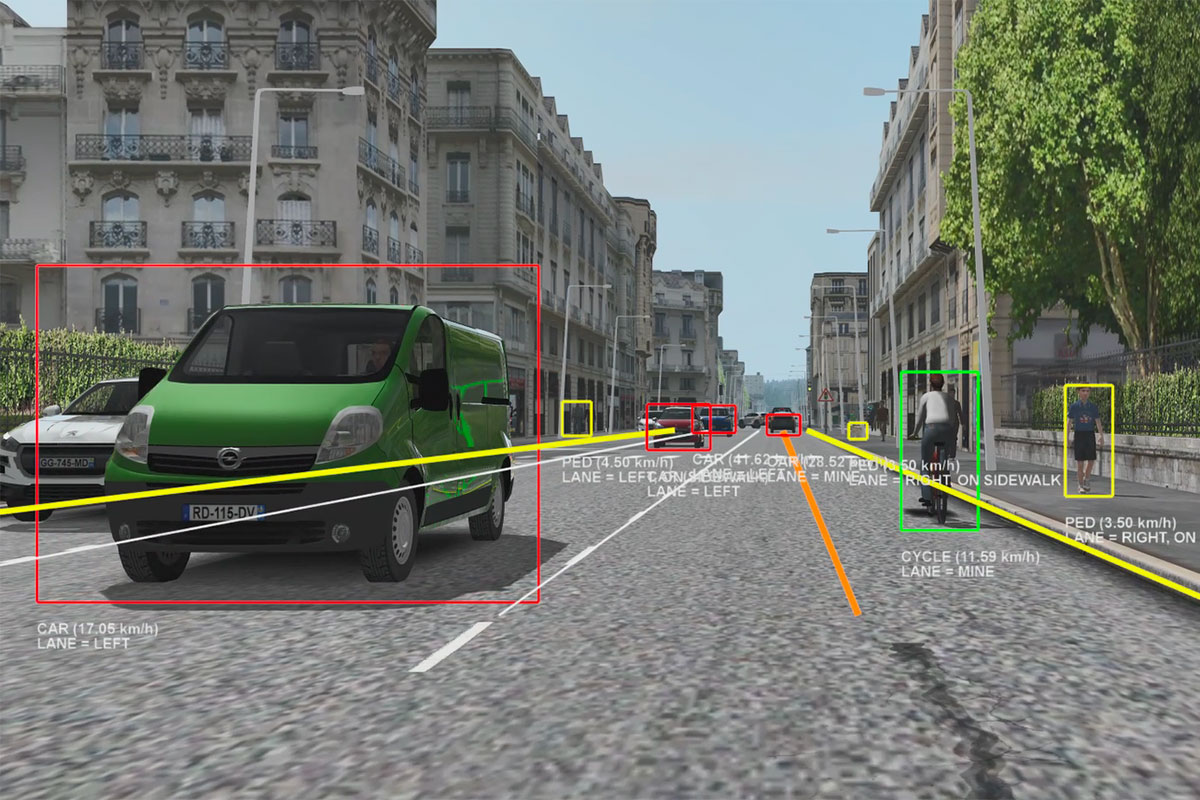
AD/ADAS
With realistic models for the vehicle, the sensors and the environment, SCANeR studio is the central development and testing platform for many ADAS and autonomous vehicle use cases:
- Active & Passive safety systems
- V2X
- HMI integration / evaluation
- Collision avoidance, Warning, Assistance systems
- Automatic parking
- Autonomous driving L3, L4, L5
- Validation
- Training
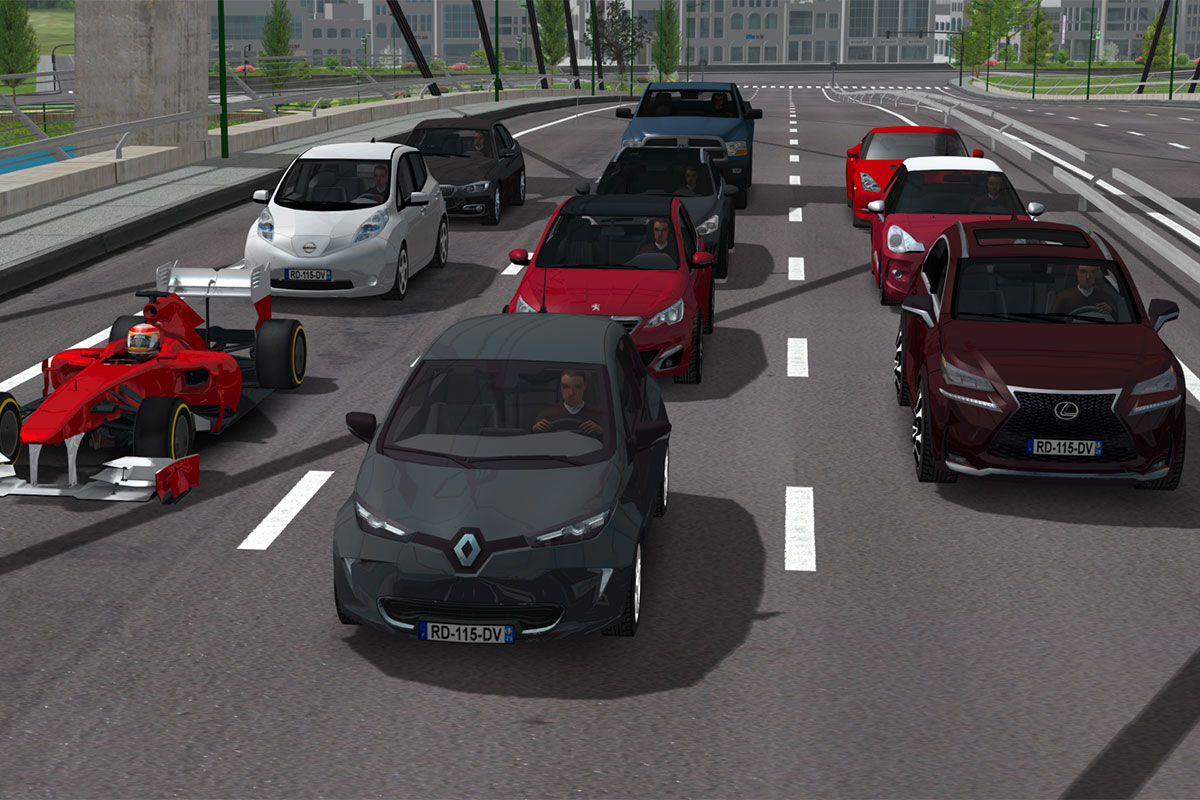
VEHICLE DYNAMICS
The SCANeR studio Essential package includes a library of the premium CALLAS vehicle dynamics models ready to be used for high-end driving simulators and automotive engineering:
- Supermini Gas/diesel/electric
- SmallFamily Gas/diesel/electric, clutch/converter/CVT
- LargeFamily Gas/diesel
- Executive standard/sport
- SUV (4×4)
- Pickup standard/sport
- Motorsport GT/GP2
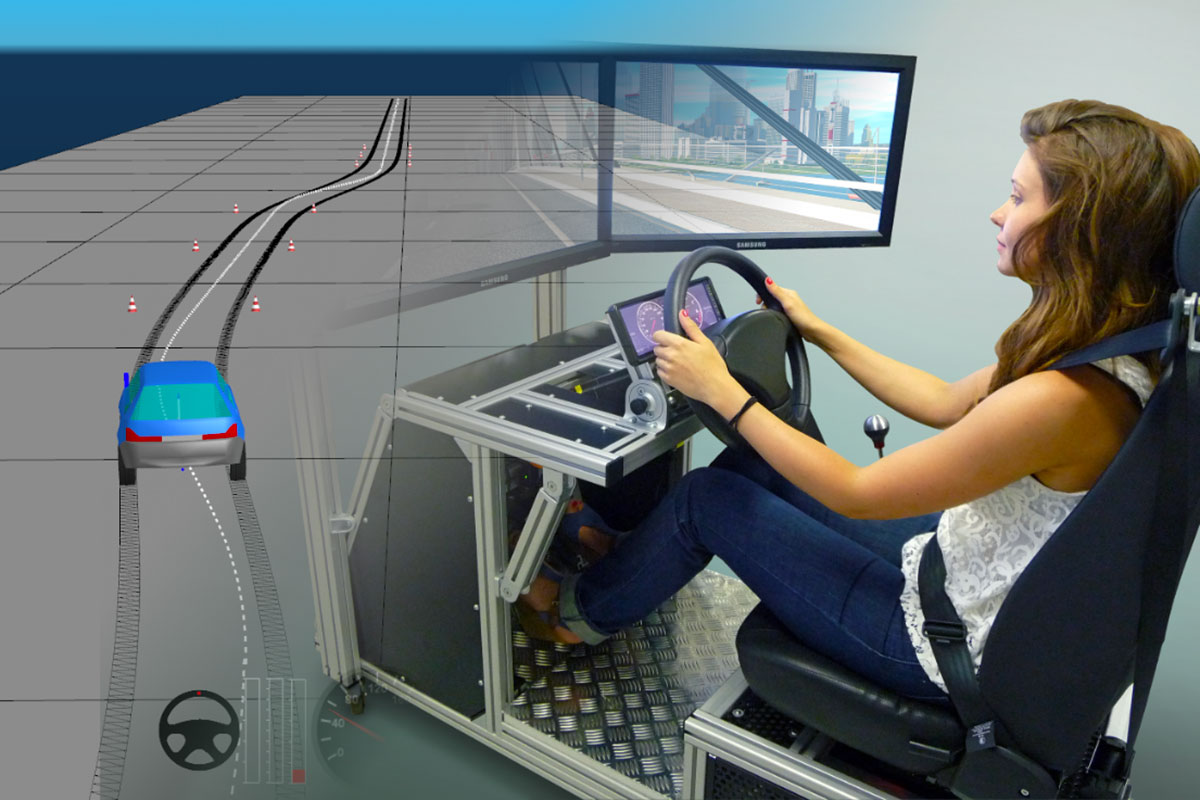
HUMAN FACTORS
Well-integrated in the development process, it allows the evaluation of the HMI system at an early stage of development and improves the relevance of Ergonomic Studies with respect to the existing tools and methods.
Use cases for human factors studies:
- Evaluation of human driver performance and behavior
- Driver fatigue, sleepiness, Hypo vigilance, drugs and alcohol effects
- Ergonomics
- Traffic safety
- Infrastructure and transportation studies
- Human Machine Interface (HMI) and ADAS
- System prototyping and integration
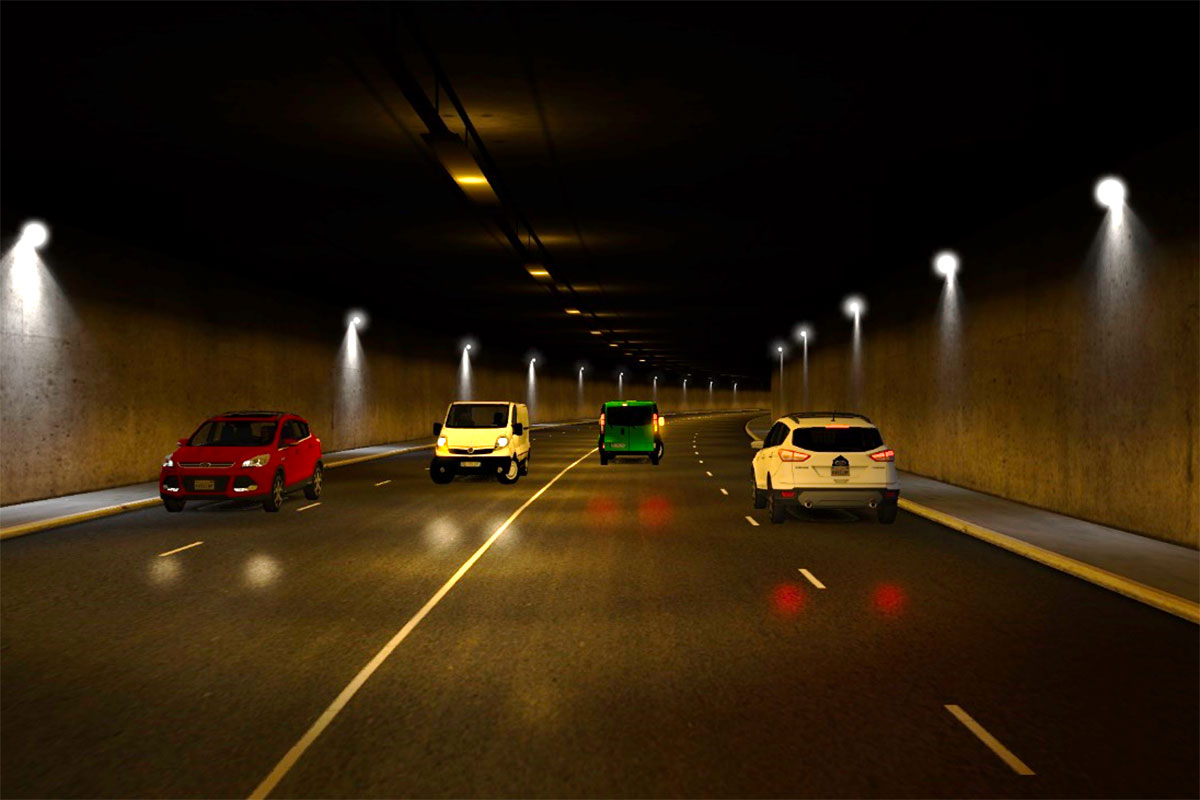
HEADLIGHTS
The headlight simulation modules of SCANeR studio are used for headlight system development and realistic night drive experiments.
Use cases for headlight simulation:
- Headlight component and system development (technology, design, cost optimization)
- Development of Intelligent lighting system laws and strategies
- AFS and ADB Matrix beam
- Night-time driving and weather conditions for road safety and comfort
- Glare and discomfort studies
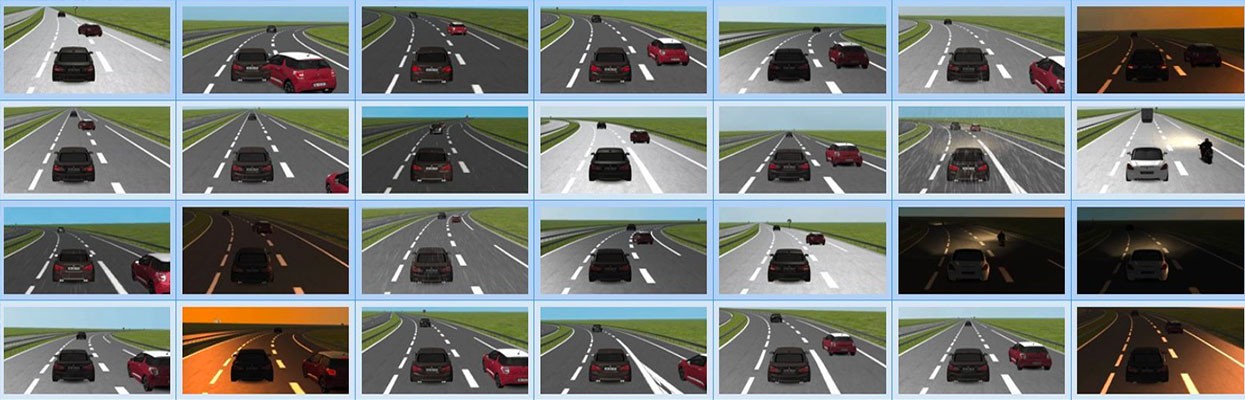
MASSIVE SIMULATION
SCANeR studio virtual platform enables driver assistance systems (ADAS) and autonomous driving functions to be endlessly tested and validated.
The use of virtual testing to complement track or road testing provides safer test condition and reduced costs and time.
This use case relies on exclusive SCANeR studio features:
- Modeling of the vehicle, sensors, driver and environment
- Complex scenario and critical events representative of real driving situations
- Automated tests edition program
- Carrying out Massive and Parallel tests in an efficient way
- Improve the validation process and tests coverage rate
- High performance computing on premises or in the cloud
- Metrics and performance analysis and reports
- Validate functional safety
Download catalogue
Do you want to receive more information?
Download the catalogue of AVSimulation after filling out the form on the side.
Please contact us!
We are the only distributors in Italy of AVSimulation
REAL-TIME SOLUTIONS FOR EVERY INDUSTRY
Real Time simulation
OPAL-RT is the world leader in the development of PC/FPGA-based real-time simulators, Hardware-in-the-Loop (HIL) testing equipment and Rapid Control Prototyping (RCP) systems to design, test and optimize control and protection systems used in power grids, power electronics, motor drives, automotive, trains, aircraft and various industries, as well as R&D centers and universities.
Power System
Automotive
Power Electronics
Aerospace
OPAL-RT TECHNOLOGIES
Real-Time Simulator
Hardware-in-the-Loop (HIL) simulation is the standard for developing and testing the most complex control, protection and monitoring systems. HIL’s rise is the result of two major factors currently affecting product development across all industries: time-to-market and system complexity.
Testing of control systems has traditionally been carried out directly on physical equipment (i.e. plant) in the field, on the full system or on a power testbed in a lab. While offering testing fidelity, this practice can be very expensive, inefficient and potentially unsafe.
HIL testing offers an excellent alternative to traditional testing methods. When performing HIL simulation, the physical plant is replaced by a precisely equivalent computer model, running in real-time on a simulator appropriately equipped with inputs and outputs (I/Os) capable of interfacing with control systems and other equipment.
In this way, the HIL simulator can accurately reproduce the plant and its dynamics, together with sensors and actuators, providing comprehensive closed-loop testing without the need for testing on real systems.
HIL offers all this functionality and more, while significantly decreasing the deficiencies of traditional testing methods.
By reducing risk, cost and the overall time required to test complex embedded systems, HIL simulation has become the standard for a great many industries around the world.
Leading the Way in Microgrid Testing
Microgrids pose unique challenges over traditional power grids: variable topologies, complex control and protection systems, an array of communication protocols and the need to interoperate multivendor equipment.
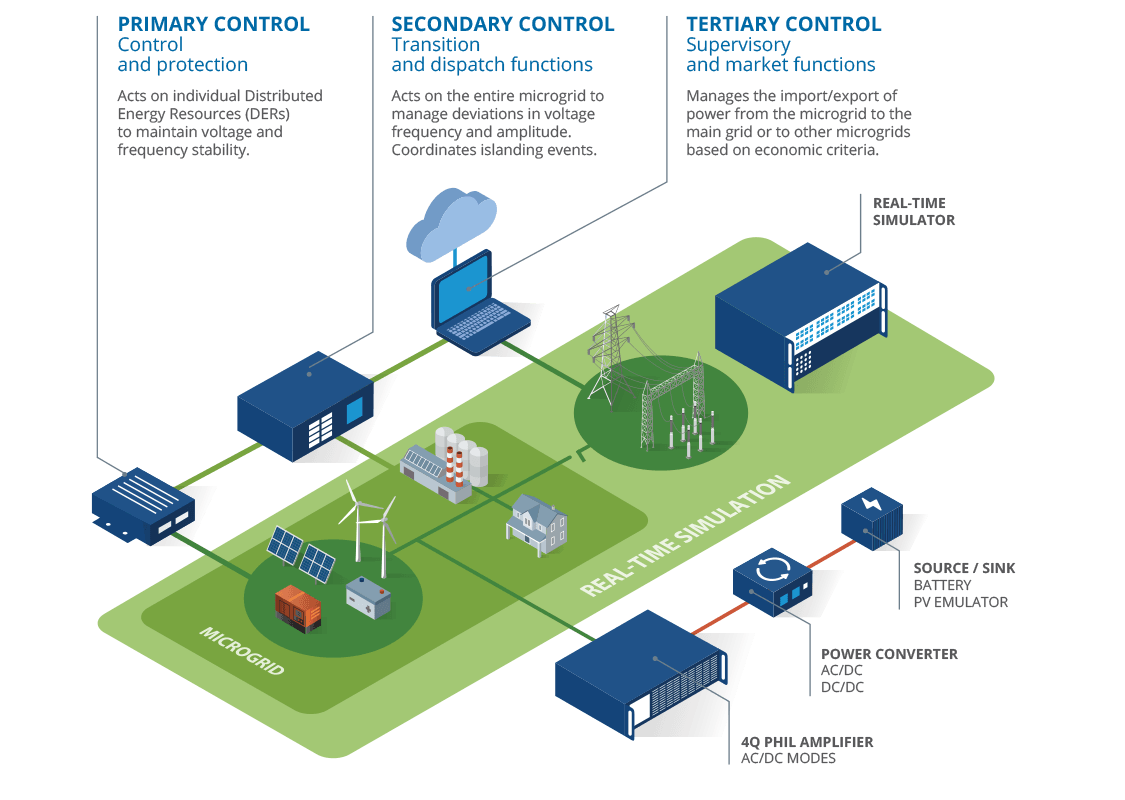
Most efficient development and testing
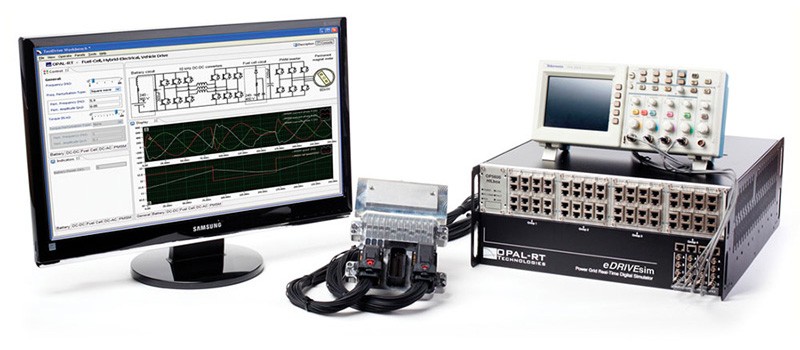
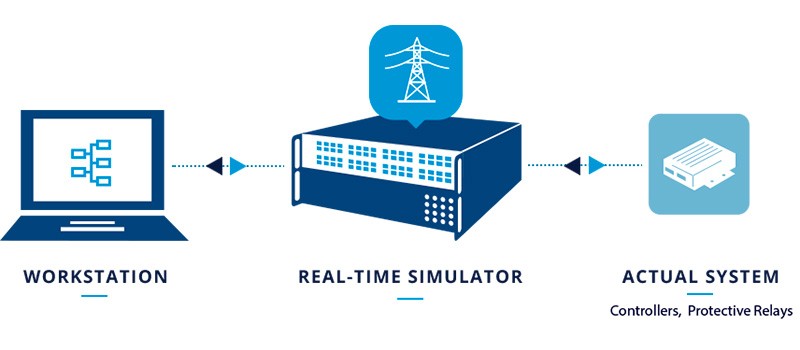
Save Time
Reduce Cost
Reduce Risk, Increase Safety
Download brochure
Do you want to receive more information?
Download the brochure of OPAL-RT after filling out the form on the side.
Please contact us!
We are the only distributors in Italy of OPAL-RT
Data Management
LIBRA
Libra streamlines complex product development, providing a cohesive platform that adapts to every industry.
It integrates real-time data from PLMs, CADs, spreadsheets and any other enterprise application, allowing project teams to set objective benchmarks, to assess progress accurately and to adjust targets with agility.
Libra facilitates a transparent overview of product development data, minimizing risks, by handling diverse BoMs (Bill of Materials) formats helping to bridge the gap between engineering, manufacturing, purchasing, sustainability, costs & financial analysis.
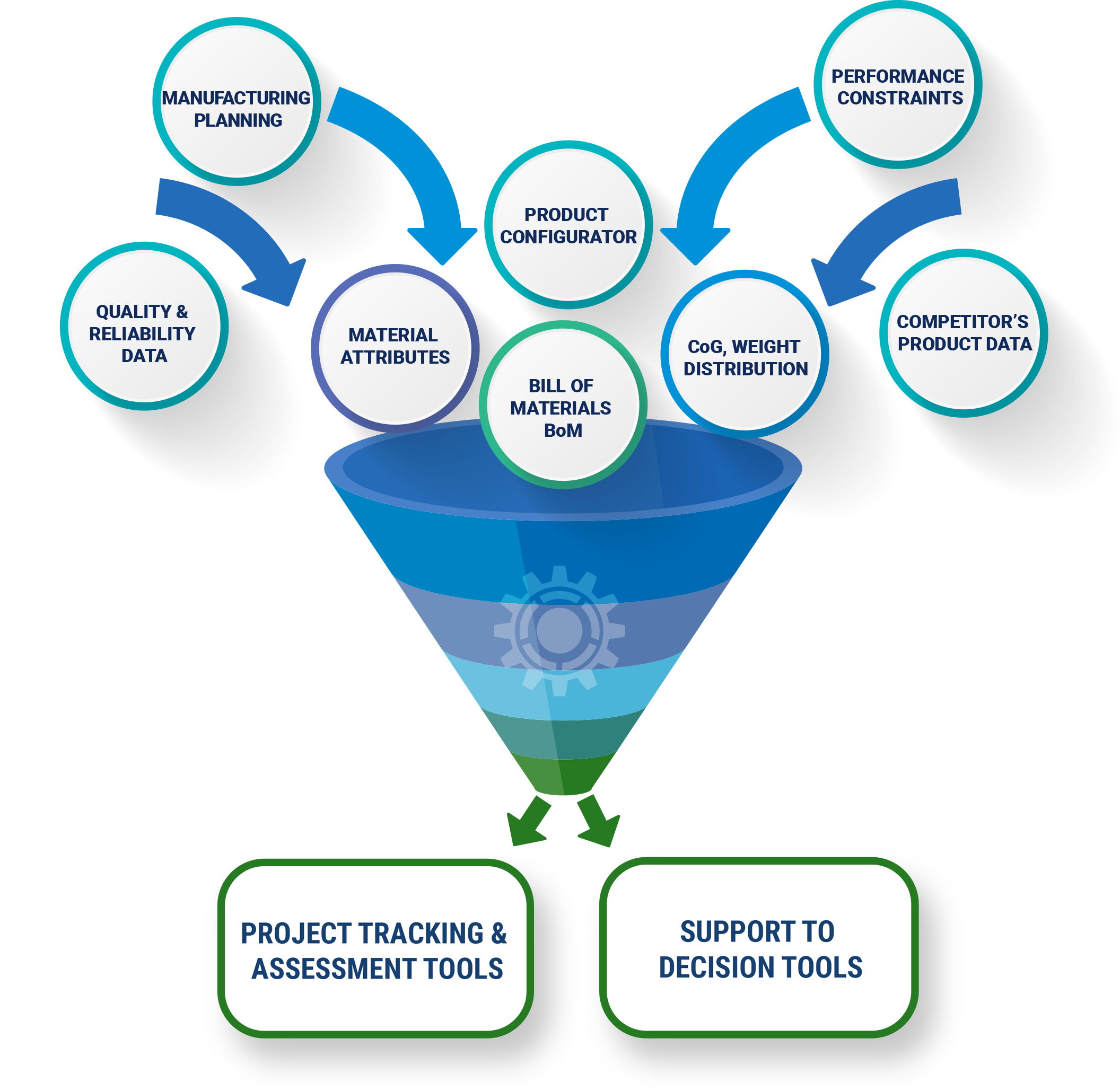