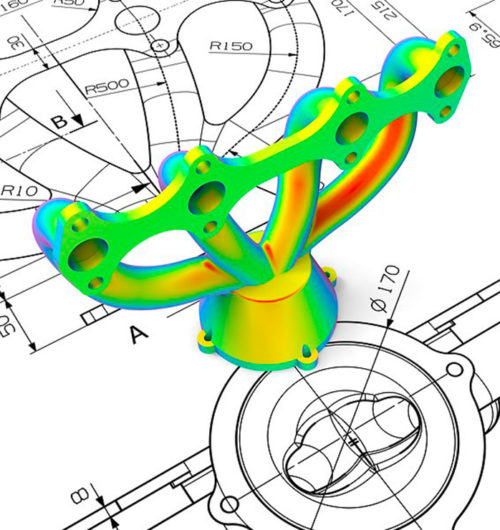
AMET has a large team of senior engineers with advanced skills and valuable experience in numerical simulation (CAE).
This know-how allows AMET to fully support and guide the complete vehicle development throughout a complete set of analyses: structural thermomechanical analysis, dynamics, fatigue strength (DSM), aerodynamics (CFD), performance analysis, acoustic analysis of automotive noise, vibration, and harshness (NVH).
Our Virtual Product engineering group is staffed with state-of-the-art HPC clusters and commercial CAE/CFD solvers, to provide each customer with the appropriate support.
AMET multidisciplinary teams provide their expertise to the Transportation industry (Automotive, Aerospace, Railways) and to all the other sectors where virtual product development is a major enabler for target achievement and time-to-market reduction.
AMET, through the use of AI in numerical simulations, offers significant advantages in improving the accuracy and reliability of results, speeds up execution times and enables the analysis of complex scenarios. Furthermore, AI optimises simulation parameters, reduces costs and stimulates innovation, accelerating time-to-market.
Virtual Analysis - CAE
Structural Simulations
Numerical simulation and virtual analysis are a very effective approach to design, test and verify components and systems, even complex ones. They can go along with and sometimes replace very expensive physical tests.
Even in the early stages of numerical methods applied to project development and product optimization, AMET has been at the forefront in exploring the possibilities offered by this approach.
Since then, tools and skills have grown to high standards and today we are able to offer our customers a wide range of applications for the different stages of the project development.
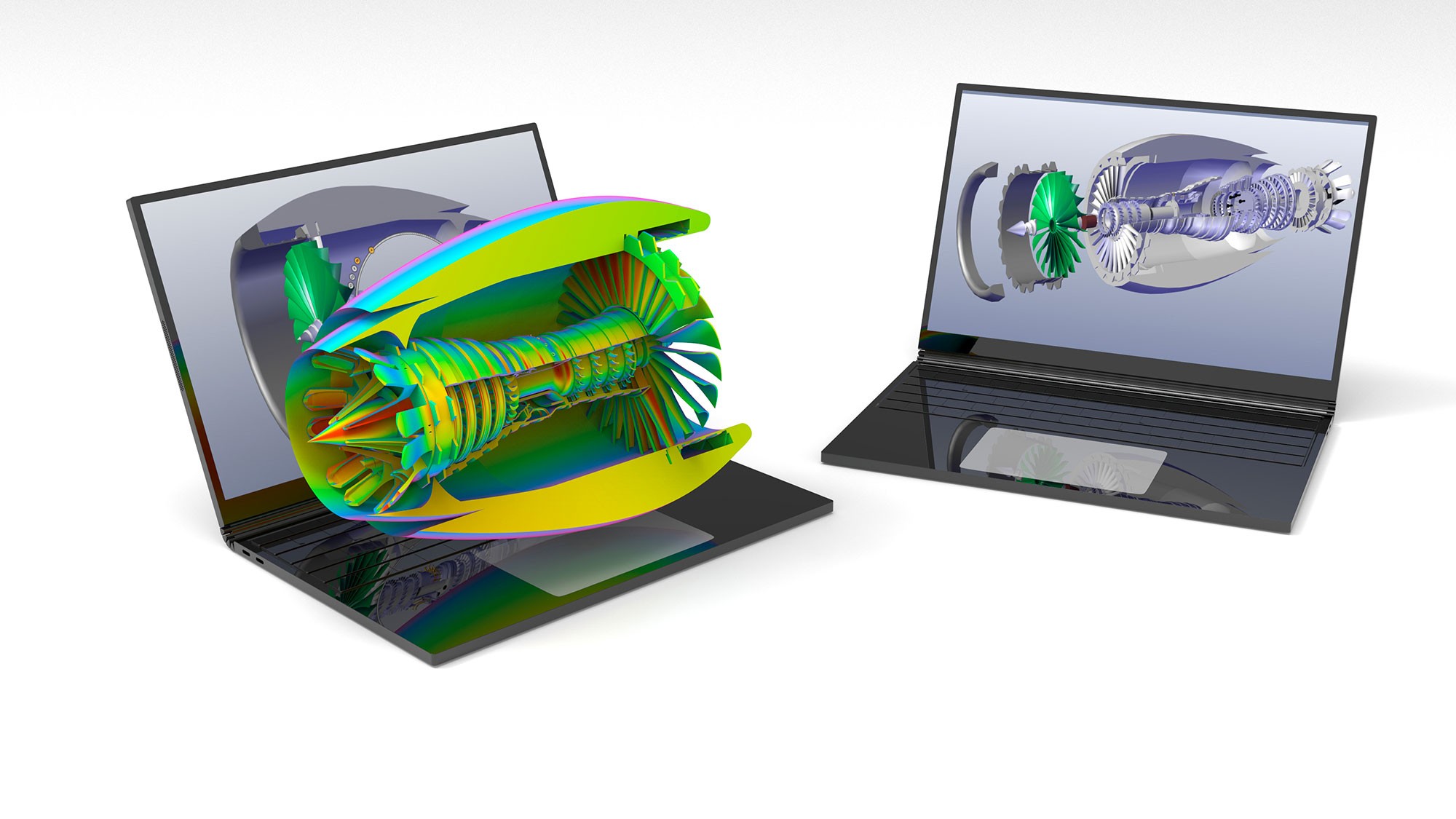
The purposes of the structural simulation can be different, depending on the objectives and the potential problems of the development process.
The main areas of application are:
Structure definition under complex loads conditions
Non conventional structures design
Topological optimization in the design of complex components and structures
Topography, size and shape optimization for weight reduction and performance achievement
Multidisciplinary optimization
Virtual Analysis - CAE
Impact Analysis & Passive Safety
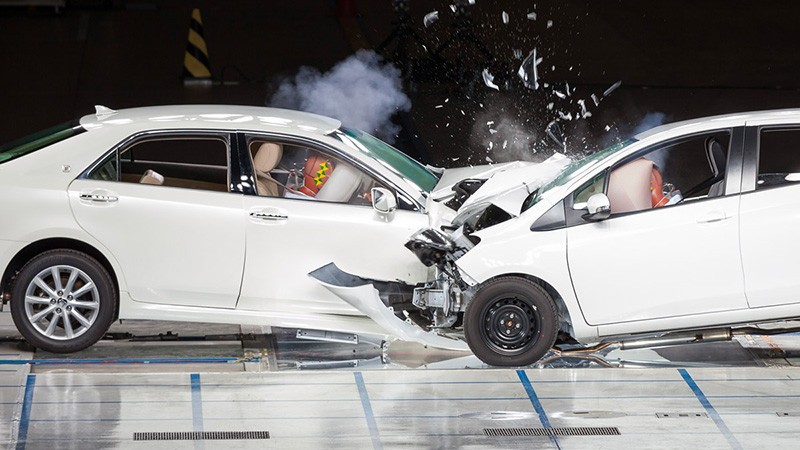
Once limited to the final checks of a vehicle project, nowadays Passive Safety is the main driver for structure design; binding regulations drive the need for virtual tests to check the design before producing any physical prototype.
AMET team employs many senior engineers with a proven experience in guiding the design to comply with the homologation or the Standard assessments, reducing the physical tests to the final project approval.
Our internal expertise covers the following loadcases:
Full vehicle crash analysis: Front, Side and Rear crash for different Markets, Standards and Ratings
Pedestrian protection
Interior impact analysis of the passenger compartment
Analysis and development of restraint systems
Roll-over analysis
Road scenarios (road barriers et similia)
Virtual Analysis - CAE
NVH
Noise, Vibration and Harshness analysis has gained an increasing importance over the years, due to customer’s more demanding comfort requests.
This is why we have devoted a great effort to enhance our skills in order to fully satisfy customers’ needs in vehicle development with challenging NVH targets.
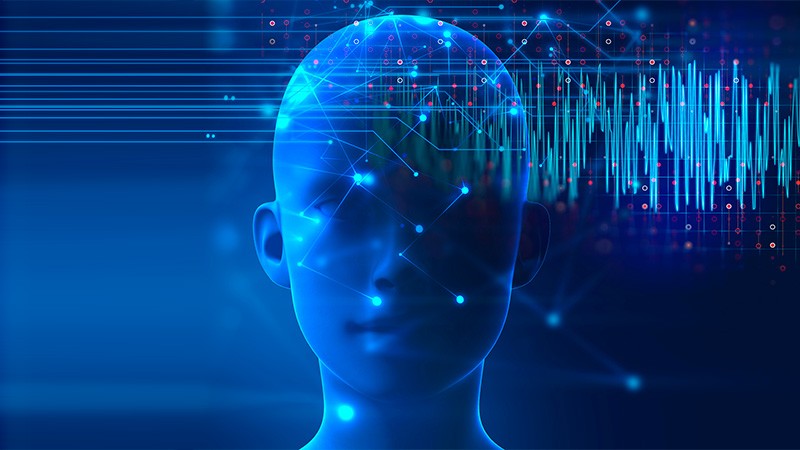
The NVH group’s expertise covers a wide range of analyses:
Modal analysis on BIW, TB and Full Vehicle
Acoustic analysis
Panel partecipation
Choice and positioning of sound-absorbing materials
SEA analysis - Statistical Energy Analysis
Virtual Analysis - CAE
DSM
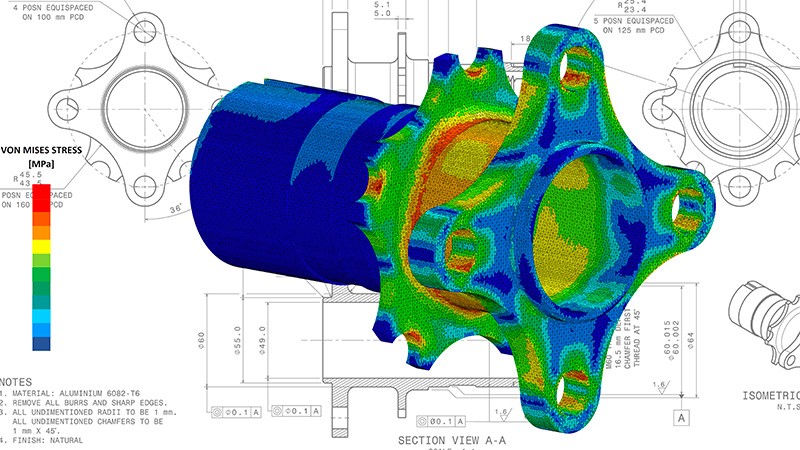
The DSM – Durability, Strength, Misuse Analysis – includes methods to verify the behavior of components and systems, mainly in terms of durability, fatigue strength and response to overloads.
AMET provides its customers with analyses aimed to evaluate functional requirements for virtual project verification, predict performance to achieve regulation targets and perform theoretical-experimental results correlation, in a multidisciplinary approach.
DSM skills cover a wide range of analyses:
Stiffness, Strength and Durability Analysis
Fatigue analysis
Buckling analysis
Highly Non-Linear Material Analysis
Thermo-Structural analysis
Virtual Analysis - CAE
Biomechanics
Together with Passive Safety, Biomechanic analysis is nowadays one of the drivers of vehicle development, with a special focus on restraints systems and on their interaction with the passenger compartment and the vehicle behaviour during the impact.
Coupling MB-FEM is being more and more used to increase the confidence on results while keeping the CPU time to a reasonable level, thus allowing more compehensive approaches like DOE analyses (Dosign Of Experiment).
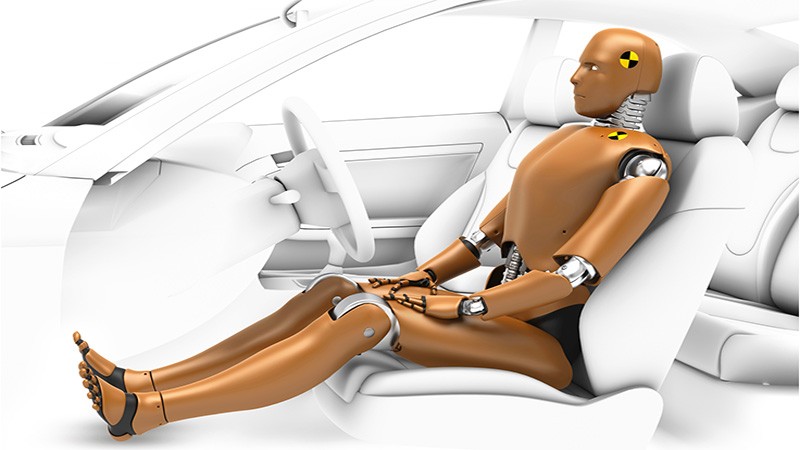
Our competence covers a wide range of activities:
Analysis and development of restraint systems (belts, DAB, PAB, Side BAG)
Seat analysis and development
CRS Analysis
Madymo Coupling with FE codes (LS-Dyna, Radioss)
Development of FEM mannequins
Virtual Analysis - CAE
CFD simulations
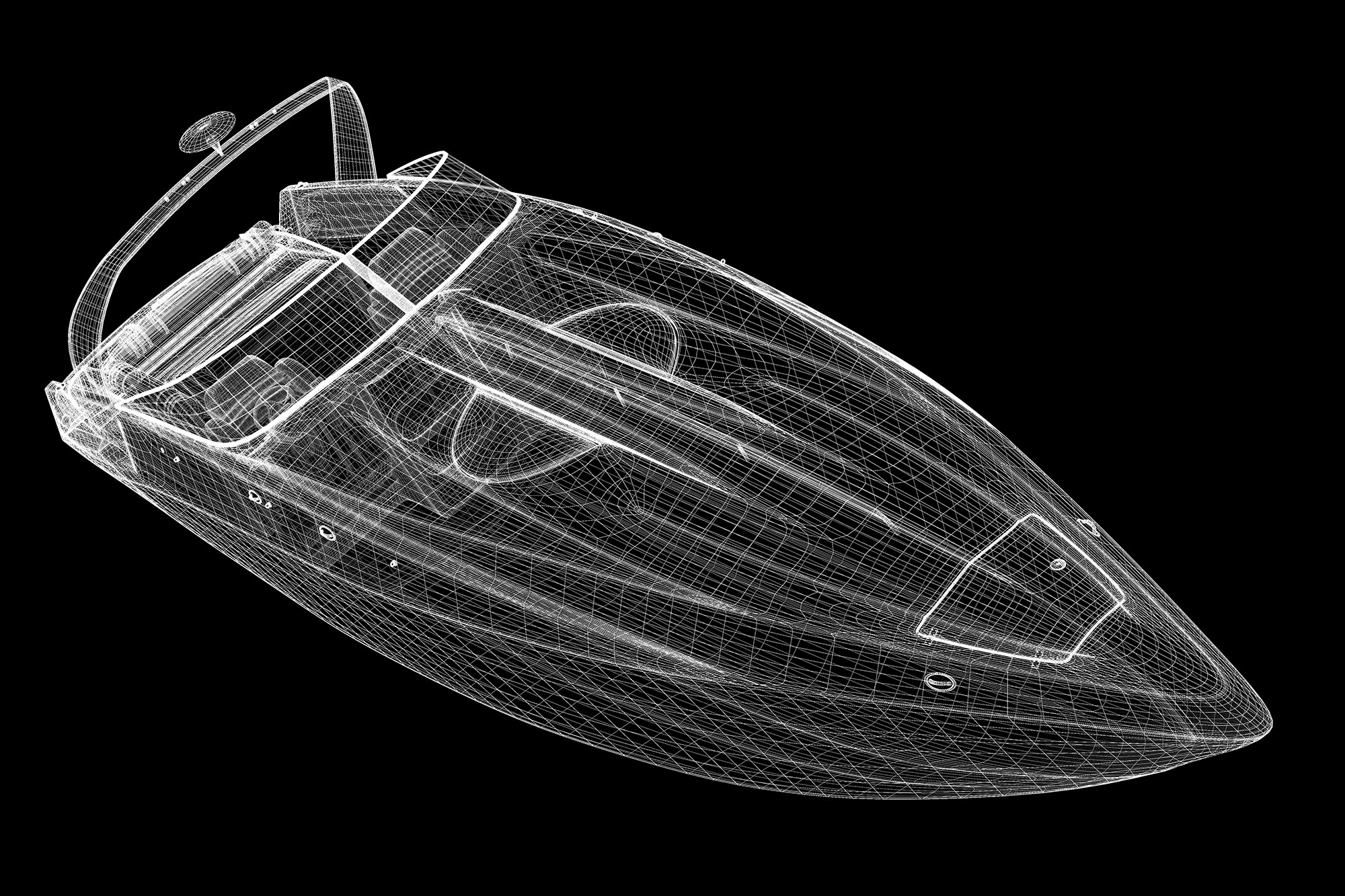
In order to reduce fuel consumption and the growing requests towards passenger compartment comfort, an increasing role is being played by Computational Fluid Dynamics.
Our strength relies on the experience to drive and test the design in a wind tunnel, thus providing our customers with a complete project development support.
Our competence covers a wide range of analyses:
Full vehicle analysis (external aerodynamics, under-hood flow & thermal analyses)
Heating, ventilation, air conditioning (HVAC) analyses and passenger thermal comfort
Components design (wings, brake cooling, lighting systems)
Powertrain cooling analysis
Wind tunnel testing support and correlation
Cooling and condensation analysis for headlights and taillights
Virtual Analysis - CAE
Vehicle dynamics
Vehicle dynamics is not just a competence, it’s our passion!
Our skills in vehicle dynamics analysis have grown over the years and our teams are now able to support the complete development process from scratch to target achievement, with simplified and detailed models.
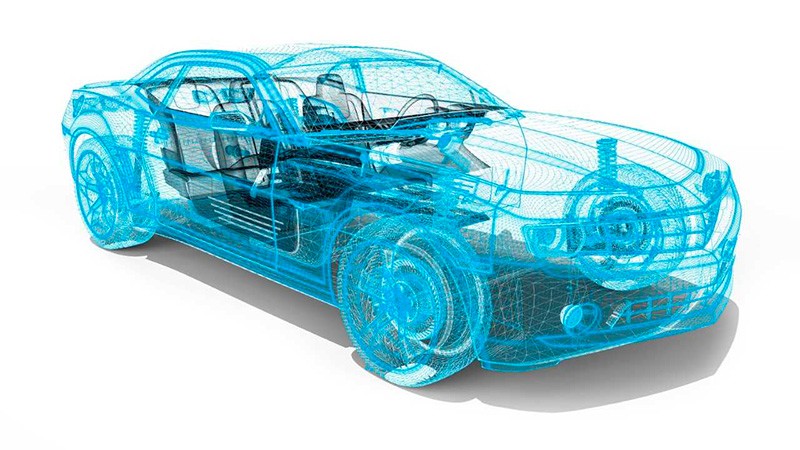
Standard activities are listed below:
Suspension development and virtual K&C
Full vehicle dynamic analysis
Roll-over scenarios analysis
Full vehicle durability analysis
Test track analysis
Real-time dynamic controls analysis
Virtual Analysis - CAE
EMC Simulations
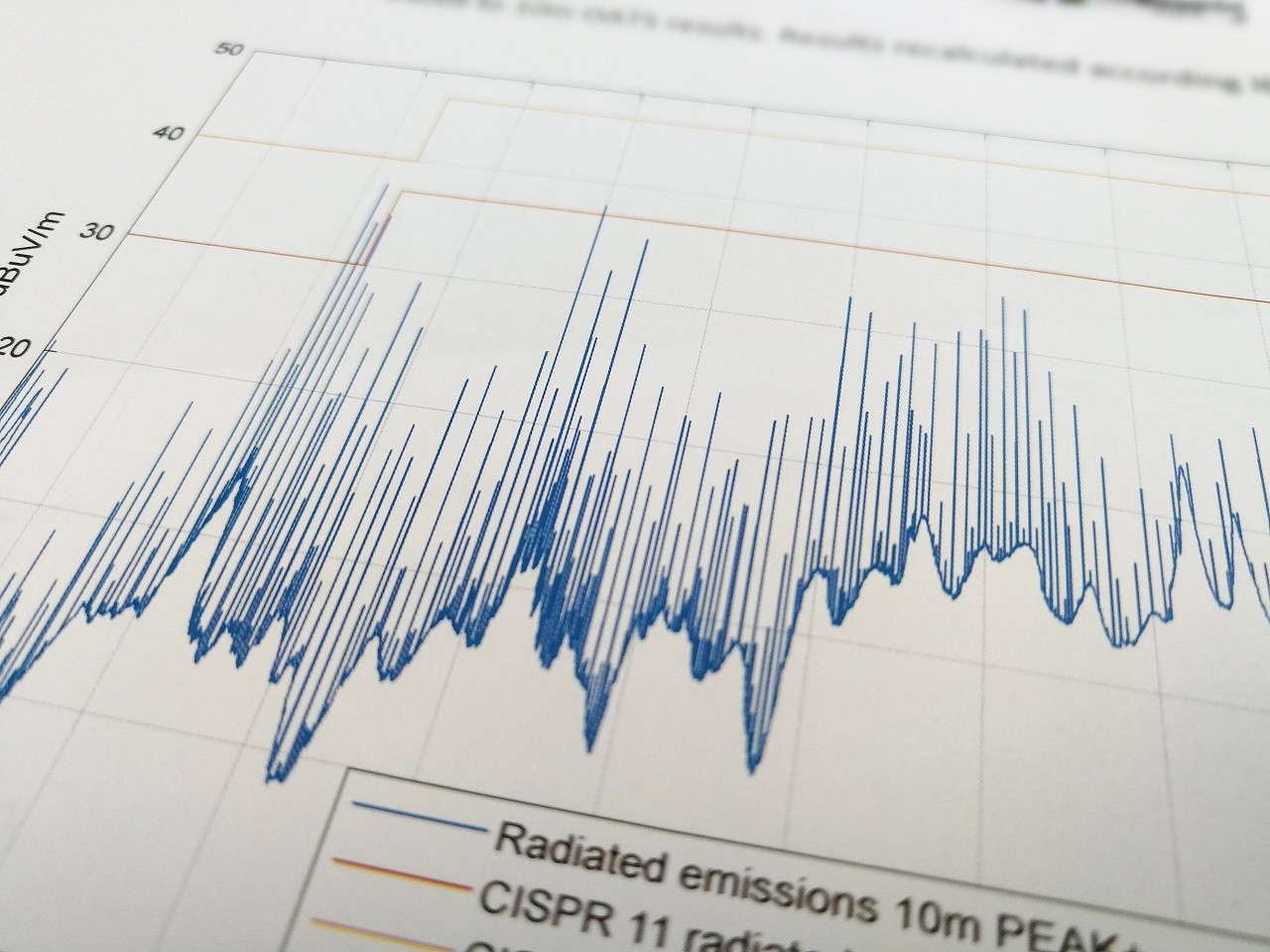
As well as computational mechanics has revolutionized design strategies, electromagnetic simulations are also becoming increasingly important to ensure help in the project phase of any electrical, electronic and electromechanical system.
With the recent spread of sustainable mobility and the related technological advances, the problems relating to electromagnetic compatibility (EMC) are assuming a role of primary importance. Thanks to computational techniques such as FEM, MoM or PEEC we are able to provide valid support, assisting the development of systems through the validation of experimental data, improvement of existing prototypes and facilitating the analysis of the problem as the complexity of the system increases.
FEM Approach to EMC problems
Integration with circuit analysis
Regulatory comparison
Analisi virtuali – CAE
Multiphisics Simulation
A multiphysics simulation is a method that integrates various physical phenomena to model and analyse complex systems.
By combining mechanical, thermal, fluid dynamic, and electromagnetic effects, it provides a more comprehensive and realistic view of the interactions between different aspects of the system.
This approach is essential in industries for optimising design and performance.
Multiphysics simulations enhance efficiency and reduce development costs, enabling more accurate predictions.
A multiphysics simulation is a method that integrates various physical phenomena to model and analyse complex systems. By combining mechanical, thermal, fluid dynamic, and electromagnetic effects, it provides a more comprehensive and realistic view of the interactions between different aspects of the system.
This approach is essential in industries for optimising design and performance. Multiphysics simulations enhance efficiency and reduce development costs, enabling more accurate predictions.
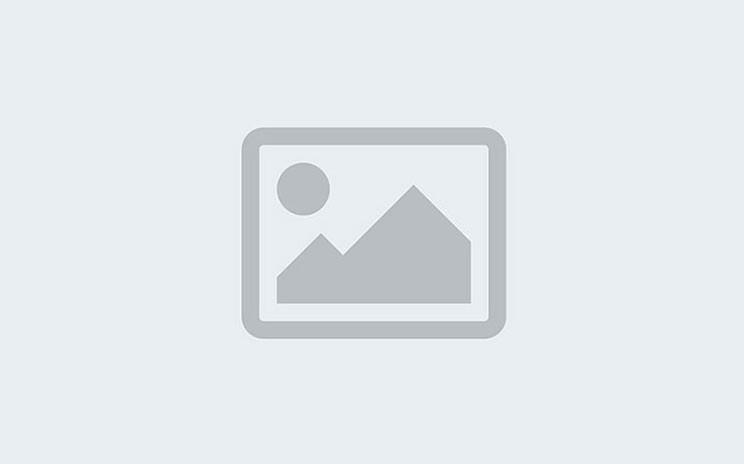